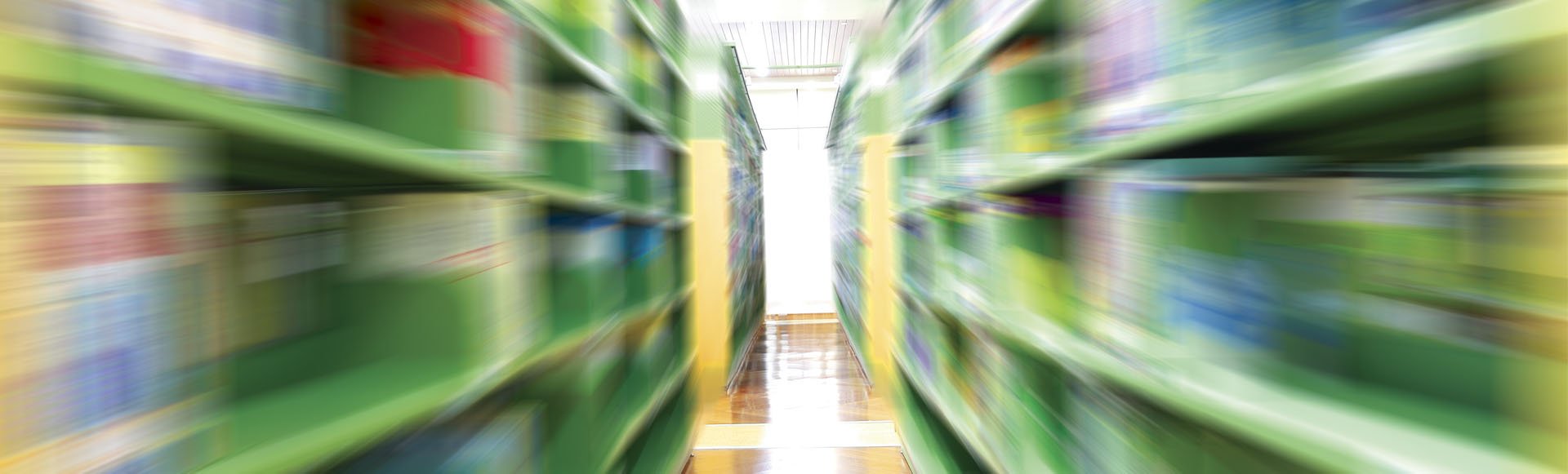
At Fuji Electric we develop products that maximize energy efficiency and lead to a responsible and sustainable society
Guide tender specifications
Guide specifications transformer based
Scope:
This general specification lays down the functional requirements, performance characteristics, quality of installation required of a ___KVA uninterruptable power system (UPS) with IGBT rectifier and inverter with inbuilt isolation transformer and with ___mins backup time.
Description of the system:
The UPS system shall consist of rectifier/charger, batteries, inverter, static bypass, manual bypass, protective devices and accessories that automatically provides continuous supply of electric power to its load within the tolerance as set out in this specifications sheet.
Project requirement:
The proposed UPS configuration is ___nos of ___KVA operating in standalone configuration or parallel redundant configuration with ___minutes backup time using sealed maintenance free VRLA battery on each UPS.
Operation modes
“Normal” mode: This is the most frequent operating condition. The energy is drawn from the primary mains power supply and is converted and used by the inverter to generate the output voltage to power the loads connected. The inverter is constantly synchronised with the auxiliary mains to enable load transfer (due to an overcurrent or inverter shutdown) without any break in the power supply to the load. The battery charger supplies the energy required to maintain or recharge the battery.
Bypass mode: In case of inverter failure, the load is automatically transferred onto the auxiliary mains without any interruption in the power supply. This procedure may occur in the following situations:
- In the event of a temporary overload, the inverter continues to power the load. If the condition persists, output is switched onto the auxiliary mains via the automatic bypass.
- Normal operation, which is from inverter, returns automatically a few seconds after the overload disappears.
- When the voltage generated by the inverter goes out of tolerances due to a major overload or a fault on the inverter
- When the internal temperature exceeds the maximum value allowed.
Battery mode: In the event of a mains failure (micro interruptions or extended black-outs), UPS continues to power the load using the energy stored in the battery. The expert battery system keeps the user constantly informed on the battery status and on the remaining backup time adapted permanently according to the battery capacity and the load rate.
Mechanical characteristics
The UPS and batteries shall be installed in cabinet(s) with an IP-20 degree of protection (standard IEC 60529)
The system shall be of modular construction and access to the subassemblies making up the system shall be exclusively through the front.
System cooling shall be by forced air ventilation and be equipped with a redundant ventilation
Environment conditions
The UPS, not including the battery, shall be capable of operating under the following environmental conditions without loss of performance:
- Temperature range during continuous operation: 0°C to 40°C(without derating)
- Maximum relative humidity: 95%
- Maximum altitude without derating: 1000 m.
- Noise level: <75 dbA
Functional & performance requirement
- The UPS system shall be of online, double conversion type conforming to IEC 62040-3
- The general & safety requirements of the UPS system shall be complied with IEC 62040-1
- The system shall be classified as VFI-SS-III as per IEC 62040 such that UPS output is independent of supply mains voltage and frequency variations
- The UPS system shall be designed to interface & operative with generator or EB mains to maintain an uninterrupted power to the loads
- The UPS System shall be constructed in heavy duty metal enclosures and designed for floor mounting
- All materials and parts comprising the UPS shall be new, of current manufacture of high grade and free from all imperfections and shall not have been in prior service, expect as required during factory testing.
- The UPS modules shall not incur permanent damages to itself or loads under all predictable fault conditions
- Static transfer switch shall be provided in the UPS. In the event of failure of UPS, the loads should be supported by static bypass without interruption
- The inverter shall be a transistorized solid state type, IGBT, which is designed with SVM Modulation Technology
- The battery shall be equipped with a self-test that can be run manually or automatically according to user-set time intervals and with configurable discharge power.
- The UPS system should have an provision to perform equalisation charging automatically on a predefined interval to maintain the healthiness of the battery
- The UPS system should be able to deliver 10% more power at 25 deg C
- The UPS shall have selfregulating and selfprotection against following conditions
- Overvoltage
- Powerline surges
- Under voltage and overcurrent induced by the mains
- Sudden changes in the output load and short circuits at the output
- Transient, surges, voltage spikes shall be suppressed and shall be removed from the output of UPS<>/li>
- The overall AC-AC efficiency of the UPS shall not be less than 94%. The efficiency shall be measured under the following conditions
- The UPS System is operating at 50% load
- The battery is fully charged and floating on the system
- The input voltage is within the specifications
- The load power factor shall be 0.9 lagging
- The UPS system shall comply with IEC 62040-2 for electromagnetic compatibility requirements
- UPS shall be compatible to take nonlinear loads and capable to handle high crest load
- UPS shall be provided with a harmonic of less than 5% and input PF of 0.99
- The UPS shall be designed to work in following environmental conditions:
- Operating temperature 0-40 deg C, continuously
- Relative humidity 0-95%
- Storage temperature: – 25°C to 50°C
- Operating altitude 1000 m above MSL
- The battery charger of the UPS should be able to adapt the battery charging based on the real time information of the status or condition of battery in terms of temperature , battery voltage, charge status etc. UPS shall be designed for minimum over load of 150% for 1 mins and 125% for 10 mins
- The rectifier should meet with the following specification in addition to other requirements stated herein.
- Input RYB phase reversal protection and correction circuit to be provided as standard to avoid UPS
transferring to battery mode in case of phase sequence change at input. The UPS should continue to work in mains mode. (If the input phase is interchanged, even then UPS has to work in double conversion mode without changing to battery mode) - The battery shall be of sealed maintenance free battery and shall be designed to support a full load for mins. An output power factor of 0.9 has to be considered for battery sizing with an ageing factor of 0.8 at an end cell voltage of 1.7V/cell
- A battery charging current of 10% of offered AH capacity has to be provided for battery charging.
- The battery may be taken out of service for maintenance, during period it shall be possible for the inverter to continue operation by drawing power from the rectifier. Ripple content at the DC link shall not exceed 2% even with battery disconnected
- The rectifiers / chargers shall be designed to completely charge the battery in a maximum time of 8 to 10 hours (Refer datasheet) after complete discharge. Facilities shall be provided to initiate battery boost charge operation by Manual or automatic means.
- Boost and float charging shall be automatically controlled to recharge the battery to 100% capacity. After battery is fully charged or after a pre-selected time (adjustable through 0 – 24 hours timer) whichever is earlier – the unit shall revert to float charge mode automatically. Also charge voltage compensation for the battery operating temperature shall be provided.
- The UPS should be capable of performing an automatic equalisation charging of the battery to improve the performance of battery
- The rectifier should meet the following specifications in addition to other requirements stated here in.
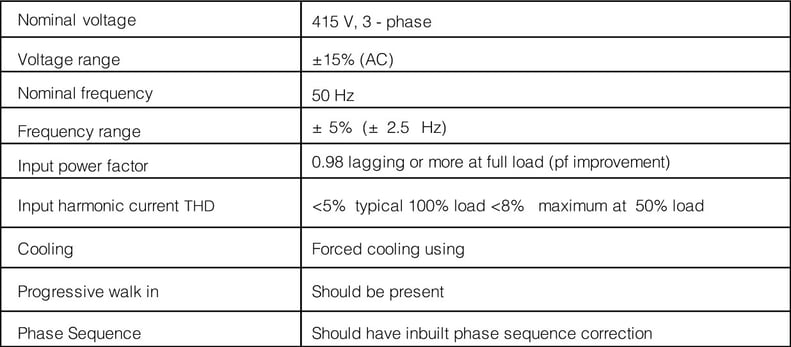
The inverter should meet the following specifications in addition to other requirements stated here in
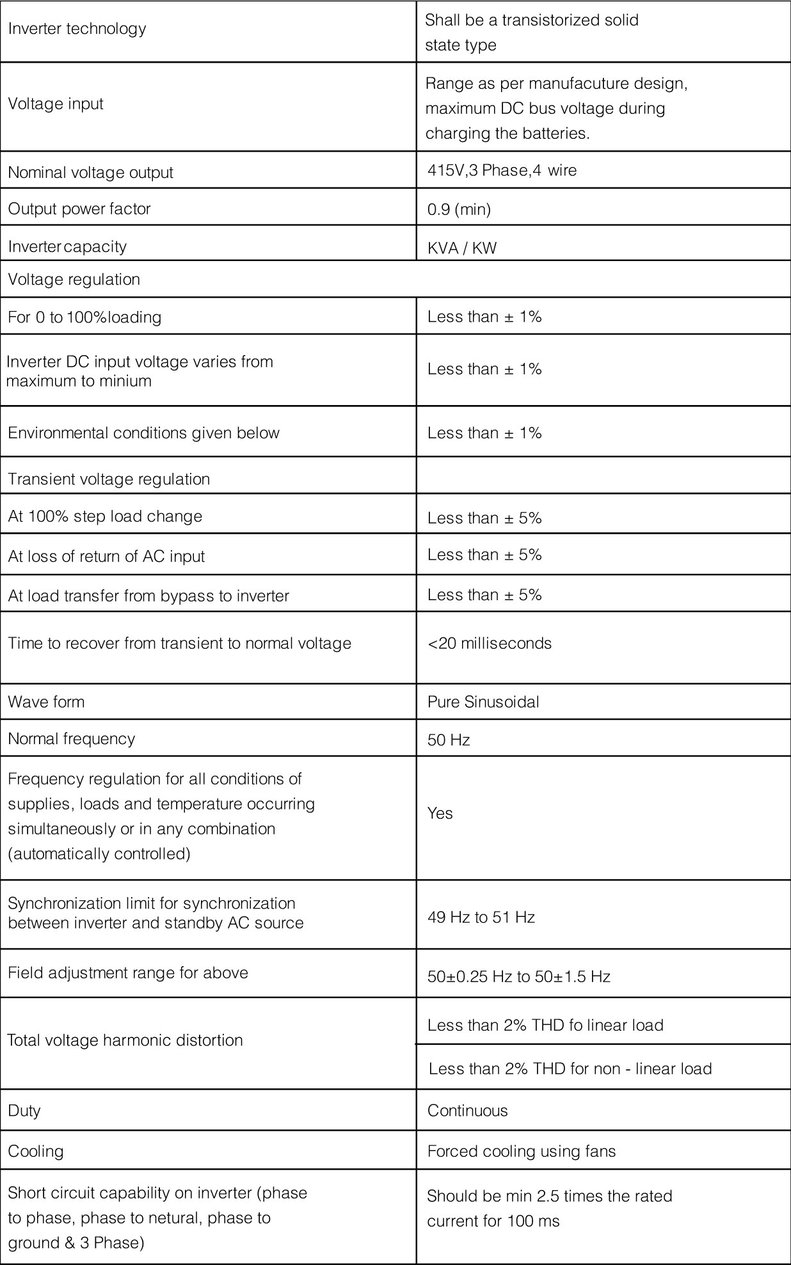
Control annunciation and indication devices: The UPS system shall have LCD Display for monitoring the parameters and status of alarm. The UPS shall be provided with a mimic diagram on the front door of cubicle housing the system.
Indications the following shall be provided:
- Monitoring of AC input voltage
- Monitoring of DC bus voltage
- Monitoring of DC charging/discharging current from the battery.
- Monitoring of output line voltage
- Monitoring of output line current
- Monitoring of input and output frequency
- Monitoring of AC bypass input voltage
- Monitoring of output power
Indications: Each UPS module shall be equipped with a mimic to indicate power flow to the critical load along with an indication of the availability of the rectifier/charger, battery, automatic bypass, inverter, and load. The mimic shall provide a quick and easy indication of the load level (displayed on LCD), including for overload conditions (displayed on LCD). This power flow is also shown in the LCD menu.
The display unit shall display the following UPS operational status
- Normal operation, load power ___%
- Battery operation, time ___minutes.
- Bypass operation.
- Standby
- LED indications for load level battery autonomy
- Indication Lamp shall be provided for Red LEDs shall be provided for ON indication, Green for OFF indication and Amber for fault indication, Main ON, Battery ON, Inverter ON, and low battery
Annunciations :
Alarm annunciation shall be provided using either LED indicators or LCD display for depiction of fault conditions in the UPS system along with audible alarm. The system shall have ‘accept’, ‘reset’ and ‘test’ facility over separate push buttons. The annunciation system shall cover the faults described earlier for the entire UPS system including in the following
- Overload
- DC overvoltage
- Emergency shutdown
- Rectifier fault
- Battery low condition
- Mains failure
- Cooling fan failure, where provided
- Fuse failure
- Static bypass ready/fault
- Static bypass inhibited
- Inverter fault
- Output voltage error
- UPS fail
- Short circuit
- Battery charging
System earthing and equipment earthing
Two independent and distinct earth electrodes shall be provided for equipment earthing of UPS connections comprising 50 x 6-mm GI strips/or as required/approved. Each of these earth electrodes shall comprise a GI plate as per Code of Practice for Earthing IS 3043-1987 (latest version).
Testing and commissioning
The UPS shall be thoroughly checked for correct operation and load tested in supplier works before dispatch. All faults, control functions and site load conditions shall be simulated, checked and proved. The equipment shall be dispatched after testing in presence of authorized representative of purchaser.
The UPS system should have intelligent test characteristic to perform a heat run test at full load and part loads without any additional load bank.
The UPS should also have an inbuilt function to perform a discharge test of the battery without any need of additional load bank.
Datasheet

Guide specifications transformerless UPS
Scope:
This general specification lays down the functional requirements, performance characteristics, quality of installation required for uninterruptable power supply(UPS)
Description of the system:
The UPS system shall consist of rectifier/charger, batteries, inverter, static bypass, manual bypass, protective devices and accessories that automatically provides continuous supply of electric power to its load within the tolerance as set out in this specifications.
Project requirement:
The critical loads covering the process load IT equipment, desktops and essential services will be backed by the proposed UPS.
The proposed UPS configuration is nos of KVA operating in standalone or parallel configuration with X minutes backup time using sealed maintenance free VRLA battery on each UPS
Operation modes
“Normal” mode: This is the most frequent operating condition. The energy is drawn from the primary mains power supply and is converted and used by the inverter to generate the output voltage to power the loads connected. The inverter is constantly synchronised with the auxiliary mains to enable load transfer (due to an overcurrent or inverter shutdown) without any break in the power supply to the load. The battery charger supplies the energy required to maintain or recharge the battery
Bypass mode: In case of inverter failure, the load is automatically transferred onto the auxiliary mains without any interruption in the power supply. This procedure may occur in the following situations:
- In the event of a temporary overload, the inverter continues to power the load. If the condition
persists, output is switched onto the auxiliary mains via the automatic bypass. - Normal operation, which is from inverter, returns automatically a few seconds after the overload disappears.
- when the voltage generated by the inverter goes out of tolerances due to a major overload
or a fault on the inverter - when the internal temperature exceeds the maximum value allowed
Battery mode: In the event of a mains failure (micro interruptions or extended blackouts), UPS continues to power the load using the energy stored in the battery. The Expert Battery System keeps the user constantly informed on the battery status and on the remaining back-up time adapted permanently according to the battery capacity and the load rate.
Mechanical characteristics
- The UPS and batteries shall be installed in cabinet(s) with an IP 20 degree of protection (standard IEC 60529)
- The system shall be of modular construction and access to the sub assemblies making up the system shall be exclusively through the front.
- System cooling shall be by forced air ventilation and be equipped with a redundant ventilation
Environment conditions
The UPS, not including the battery, shall be capable of operating under the following environmental conditions without loss of performance:
- Temperature range during continuous operation: 0°C to 40°C
- Maximum relative humidity: 95%
- Maximum altitude without derating: 1000 m.
- Noise level: <70 dbA
Functional & performance requirement
- The UPS System shall be of online, double conversion type conforming to IEC 62040-3
- The general & safety requirements of the UPS system shall be complied with IEC 62040-1
- The system shall be classified as VFI-SS-III as per IEC 62040 such that UPS output is independent of supply mains voltage and frequency variations
- The UPS system shall be designed to interface & operative with generator or EB mains to maintain an uninterrupted power to the loads
- The UPS System shall be constructed in heavy duty metal enclosures and designed for floor mounting
- All materials and parts comprising the UPS shall be new, of current manufacture of high grade and free from all imperfections and shall not have been in prior service, expect as required during factory testing.
- The UPS modules shall not incur permanent damages to itself or loads under all predictable fault conditions
- Static transfer switch shall be provided in the UPS. In the event of failure of UPS, the loads should be supported by static bypass without interruption
- The Inverter shall be a transistorized solid state type, IGBT, which is designed with SVM modulation technology
- The battery shall be equipped with a self-test that can be run manually or automatically according to user-set time intervals and with configurable discharge power.
- The UPS system should have an provision to perform equalisation charging automatically on a predefined interval to maintain the healthiness of the battery
- The UPS system should be able to deliver 10% more power at 25 deg C
- The UPS shall have self-regulating and self-protection against following conditions
- Over voltage
- Power line surges
- Under voltage and over current induced by the mains
- Sudden changes in the output load and short circuits at the output
- Transient surges, voltage spikes shall be suppressed and shall be removed from the output of UPS
- The overall AC-AC efficiency of the UPS shall not be less than 95%. The efficiency shall be measured under the following conditions
- The UPS system is operating at 50% load
- The battery is fully charged and floating on the system
- The input voltage is within the specifications
- The load power factor shall be 0.9 lagging
- The battery shall be of sealed maintenance free battery and shall be designed to support a full load for X mins. An output power factor of 0.9 has to be considered for battery sizing with an ageing factor of 0.8 at an end cell voltage of 1.7V/cell
- A battery charging current of 10% of offered AH capacity has to be provided for battery charging.
- The battery may be taken out of service for maintenance, during which period it shall be possible for the inverter to continue operation by drawing power from the rectifier. Ripple content at the DC link shall not exceed 2% even with battery disconnected
- The rectifiers/chargers shall be designed to completely charge the battery in a maximum time of 8 to 10 hours (Refer datasheet) after complete discharge. Facilities shall be provided to initiate battery boost charge operation by manual or automatic means.
- Boost and float charging shall be automatically controlled to recharge the battery to 100% capacity. After battery is full charged or after a pre-selected time (adjustable through 0- 24 hours timer) whichever is earlier, the unit shall revert to float charge mode automatically. Also charge voltage compensation for the battery operating temperature shall be provided.
- The rectifier should meet the following specifications in addition to other requirements stated here in
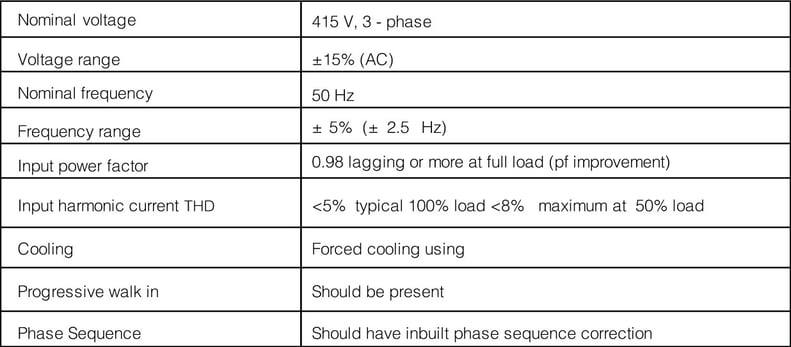
The inverter should meet the following specifications in addition to other requirements stated here in.
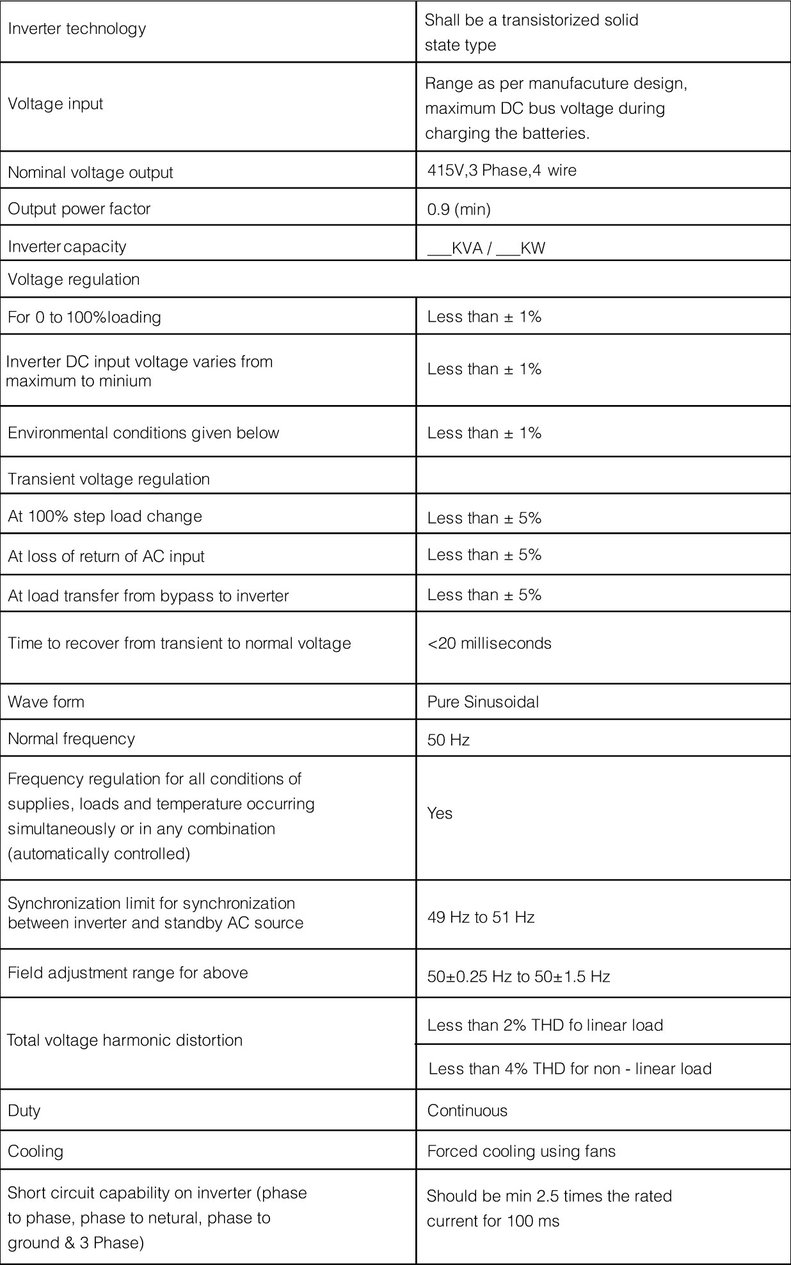
Control annunciation and indication devices: The UPS system shall have LCD Display for monitoring the parameters and status of alarm. The UPS shall be provided with a mimic diagram on the front door of cubicle housing the system.
Indications : The following shall be provided
- Monitoring of AC input voltage
- Monitoring of DC bus voltage
- Monitoring of DC charging/discharging current from the battery.
- Monitoring of output line voltage
- Monitoring of output line current
- Monitoring of input and output frequency
- Monitoring of AC bypass input voltage
- Monitoring of output power
Indications: Each UPS module shall be equipped with a mimic to indicate power flow to the critical load along with an indication of the availability of the rectifier/charger, battery, automatic bypass, inverter and load. The mimic shall provide a quick and easy indication of the load level (displayed on LCD), including for overload conditions (displayed on LCD). This power flow is also shown in the LCD menu.
The display unit shall display the following UPS operational status
- Normal operation, load power ___%
- Battery operation, time ___minutes.
- Bypass operation.
- Standby
- LED indications for load level battery autonomy
- Indication lamp shall be provided for Red LEDs shall be provided for ON indication, Green for OFF indication and Amber for fault indication, Main ON, Battery ON, Inverter ON, and low battery
Annunciations :
Alarm annunciation shall be provided using either LED indicators or LCD display for depiction of fault conditions in the UPS system along with audible alarm. The system shall have ‘accept’, ‘reset’ and ‘test’ facility over separate push buttons. The annunciation system shall cover the faults described earlier for the entire UPS system including in the following
- Overload
- DC over voltage
- Emergency shutdown
- Rectifier fault
- Battery low condition
- Mains failure
- Cooling fan failure, where provided
- Fuse failure
- Static bypass ready/fault
- Static bypass inhibited
- Inverter fault
- Output voltage error
- UPS fail
- Short Circuit
- Battery charging
System earthing and equipment earthing
Two independent and distinct earth electrodes shall be provided for equipment earthing of UPS connections comprising 50×6-mm GI strips/ or as required/ approved. Each of these earth electrodes shall comprise a GI plate as per Code of Practice for Earthing IS 3043-1987 (latest version)
Testing and commissioning
The UPS shall be thoroughly checked for correct operation and load tested in supplier works before dispatch. All faults, control functions and site load conditions shall be simulated, checked and proved. The equipment shall be dispatched after testing in presence of authorized representative of purchaser.
The UPS system should have intelligent test characteristic to perform a heat run test at full load and part loads without any additional load bank
The UPS should also have an inbuilt function to perform a discharge test of the battery without any need of additional load bank

Modular UPS system
Description
The UPS shall consist of rectifier/charger, battery, inverter, static transfer switch, maintenance bypass Switch, Synchronizing Equipment, Protective Device and other Accessories. The UPS shall provide continuous electric power within specified tolerance, without interruption, to the critical loads.
Normally electrical energy from normal plant power source shall be supplied to UPS System.
The Solid State Rectifier/charger shall convert incoming AC power to DC power. The rectifier / charger output shall be fed to Solid State Inverter. The inverter shall convert the DC power into AC power, which shall supply the load. Upon failure of AC power, input power for inverter shall automatically be supplied from the battery with no interruption/disturbance in inverter output in excess of limits specified herein (in these specifications).
At the same time, UPS shall energize an alarm circuit. The duration for which Battery shall supply A/C power to O/P shall be minimum 15 minutes.
When A/C power is restored, the input power for the inverter and for recharging the battery shall automatically be supplied from rectifier / charger output without interruption/disturbance in inverter output in excess of limits specified herein (in these specifications).
The Solid State Circuitry used for both rectifier & inverter shall be IGBT technology.
Intelligent RS-232 Communication shall be possible which will Provide UPS status indications, electrical parameters such as Input & Output Voltage, Load levels etc and unattended shutdown.
User-friendly LCD Display to indicate all important UPS parameters such as input voltage, output voltage, battery level and load level shall be provided.
The UPS system shall consist of the following modular architecture
Architecture
Operation mode
“Normal” mode. This is the most frequent operating condition. The energy is drawn from the primary mains power supply and is converted and used by the inverter to generate the output voltage to power the loads connected. The inverter is constantly synchronised with the auxiliary mains to enable load transfer (due to an overcurrent or inverter shutdown) without any break in the power supply to the load. The battery charger supplies the energy required to maintain or recharge the battery.
Bypass mode: In case of inverter failure, the load is automatically transferred in to the auxiliary mains without any interruption in the power supply. This procedure may occur in the following situations:
- In the event of a temporary overload, the inverter continues to power the load. If the condition persists, output is switched in to the auxiliary mains via the automatic bypass.
- Normal operation, which is from inverter, returns automatically a few seconds after the overload disappears.
- when the voltage generated by the inverter goes is out of tolerances due to a major overload or a fault on the inverter
- when the internal temperature exceeds the maximum value allowed.
Battery mode: In the event of a mains failure (micro interruptions or extended blackouts), UPS continues to power the load using the energy stored in the battery. The expert battery system keeps the user constantly informed on the battery status and on the remaining backup time adapted permanently according to the battery capacity and the load rate.
Architecture
Control modules
The system should not have an centralized control modules, the control modules has to be built in each power module to improve the reliability of the system
Static switch
The modular UPS system that the bidders provide shall use concentrated bypass and the bypass module shall be hot swappable. A built-in bypass shall be provided
Modular UPS system
Scalable power modules
The system shall be comprised of 25/30 kVA power modules and shall be capable of being configured for N+X redundant operation and power modules should be hot swappable to facilitate the scalability without any disturbance to load.
Module management:
The modular UPS shall offer the ability to scale its capacity and/or redundancy by automatically shifting load to fewer power modules and selectively place unnecessary modules in the “hibernate mode” based on the sensed output load level. This is in order to drive the load higher on the remaining modules. Therefore, with multiple modules, a UPS shall achieve 2-3% higher efficiencies than conventional operation when loaded less than 50% of system rating. In case of instantaneous addition of full load on the bus, this modules should assume load without any interruption to the total load.
A power module shall not be restricted to any specific slot. Power modules can be installed without having to pre-configure. Configuration shall be entirely automated.
Eco mode:
In bypass operation, an even higher operating efficiency may be achieved without sacrificing protection when there are good power conditions. Depending on configuration, efficiency can exceed 99%.The load remains in bypass mode until the input voltage exceeds tolerance levels, and then enters full protection mode. This setting is disabled by default and can be configured using the display.
Load test at site:
UPS should have the ability to perform a full load test in double conversion mode without the connection of a load bank.
Phase sequence correction
Fault tolerance:
The combination of the modular UPS and the parallel redundant architecture shall confine the component or PCB failures to a single power module. The remainder of the system power modules shall not be affected and shall continue to provide protection to the critical load. With the N+1 parallel redundant architecture, the UPS faulty power module is isolated from the working units thus providing the system fault tolerance.
Phase sequence correction
The system should have inbuilt phase sequence correction and should continue to operate in mains mode
Efficiency
The overall AC-AC efficiency of the UPS shall be not be less than 95%.The efficiency shall be measured under the following conditions
- The UPS System is operating at 50% load
- The battery are fully charged and floating on the system
- The input voltage is within the specifications
- The load power factor shall be 0.9 lagging
Environmental conditions
The UPS shall be designed to work in following environmental conditions:
- Operating temperature 0-40 deg C
- Relative Humidity 0-95%
- Storage temperature : – 25°C to 50°C
- Operating altitude 1000m above MSL
Display and metering
The UPS system shall have LCD Display for monitoring the parameters and status of alarm. The UPS shall be provided with a mimic diagram on the front door of cubicle housing the system. The failure of display should not lead to the system failure. The system should work normally without the display.
Indications: Each UPS module shall be equipped with a mimic to indicate power flow to the critical load along with an indication of the availability of the rectifier/charger, battery, automatic bypass, inverter and load. The mimic shall provide a quick and easy indication of the load level (displayed on LCD), including for overload conditions (displayed on LCD). This power flow is also shown in the LCD menu.
The display unit shall display the following UPS operational status
- Normal operation, load power ____%
- Battery operation, time ____minutes.
- Bypass operation.
- Standby
- LED indications for load level battery autonomy
Indication Lamp shall be provided for Red LEDs shall be provided for ON indication, Green for OFF indication and Amber for fault indication, Main ON, Battery ON, Inverter ON, and Low Battery. Each power module shall also have its own display,
The following parameters of each power module.
- Monitoring of AC input voltage
- Monitoring of DC bus voltage
- Monitoring of DC charging/discharging current from the battery.
- Monitoring of output line voltage
- Monitoring of output line current
- Monitoring of AC input voltage
- Monitoring of DC bus voltage
- Monitoring of DC charging/discharging current from the battery.
- Monitoring of output line voltage
- Monitoring of output line current
- Monitoring of input and output frequency
- Monitoring of AC bypass input voltage
- Monitoring of output power
Isolated Power Supply
Annunciations :
Alarm annunciation shall be provided using either LED indicators or LCD display for depiction of fault conditions in the UPS system along with audible alarm. The system shall have ‘accept’, ‘reset’ and ‘test’ facility over separate push buttons. The annunciation system shall cover the faults described earlier for the entire UPS system including in the following
- Overload
- DC overvoltage
- Emergency shutdown
- Rectifier fault
- Battery low condition
- Mains failure
- Cooling fan failure, where provided
- Fuse failure
- Static bypass ready/fault
- Static bypass inhibited
- Inverter fault
- Output voltage error
- UPS fail
- Short circuit
- Battery charging
Reference standards
The static uninterruptible power system must be designed and produced in compliance with the following international standards
- EN 62040-1 “General and safety requirements for UPS used in operator access areas”
- EN 62040-2 “Electro Magnetic Compatibility requirements (EMC)”
- EN 62040-3 “Performance requirements and test methods”
Datasheet

Isolated Power Supply
Design, Manufacture, Testing, Supply and supervision for installation and commissioning of 5KVA, 8KVA & 10KVA Medical Isolation Panel for OTs, ICU/ICCUs & NICUs as per IEC 60364-7-710 & BIS SP-30 Part-3 Section-IV consisting of following:
A medical ungrounded (IT) system shall be designed with 230VAC 63A, 10KA input MCB, Input Voltmeter & Ammeter, 5KVA/8KVA/10KVA 230/230 VAC single phase Medical isolation transformer according to IEC 61558-2-15 (safety of power transformers, power supply units and similar – part 2 – 15: Particular requirements for isolating transformers for the supply of medical locations.) in conformance to additional requirements of IEC 60364-7-710 (Electrical installations of buildings – requirements of special installations or locations – Medical locations) for low leakage at secondary side including provision for overload and high conformance to IEC 61557-8 (Electrical safety in low voltage distribution systems up to 1000V AC and 1500 VDC – Equipment for Testing, Measuring or monitoring of protective measures – part 8: Insulation monitoring devices for IT systems.) and IEC 60364-7-710, 12nosof 230 VAC, 20A, 1KA, DP MCB for load distribution, with on-line 12- channel insulation fault location system in conformance to IEC 61557-9 for medical locations. All the above devices shall be installed and prewired in MS CRCS fabricated Panel painted to Grey Shade, fan cooled, cable entry from top ready for installation at hospital premises. Separate Remote Alarm Indicator for display of Insulation, transformer Overload and temperature alarm and other status indications at remote suitable location.
1.0 Scope:
This specification covers the design and requirements for electrical safety in critical rooms (Group 2) like
Operation Theatres,
Intensive Care Units, Anaesthetic Rooms and Premature Baby Rooms in hospitals and medical
establishments as per
IEC 60364-7-710 and Provision P5 as per IS-SP30-Part 3Section 4-2011.
2.0 Reference Standards:
IEC 60364-7-710: Electrical installation of buildings – Requirements for special installations locations – Medical locations IS SP30 2011-India: Part-3, Section-4: Medical establishments
3.0 Introduction:
In hospitals and in medical locations safe and secure power supply to mains supplied equipment intended to be used for life-saving and life-supporting measures which affect the health and safety of patients in case of failure or by current passing through the human body due to leakage.
Medical locations are divided into 3 groups as per IEC-60364-7-710 considering the application of medical technical equipment on the patient. Group 0, Group 1 and Group 2. In IS- NEC-SP-30-2011 all Hospital locations are categorised under seven groups of safety provisions namely P0 to P7. Operation Theatres, Intensive Care Units, Premature Baby Rooms, Anesthetic Rooms etc. are categorized under safety provision P5. Therefore P5 category locations as per NEC & Group 2 medical locations as per IEC are critical areas, because a failure of the power supply or leakage currents higher than 10 ìA passing through the dissected human body & discontinuity (failure) of the supply can lead to an immediate threat to the life and limb of the patient. Group 2 or P5 category locations are Anaesthetic rooms, Operating theatres, Heart catheterization rooms, Angiographic room, Intensive care rooms, Premature baby rooms etc.
4.0 Requirements:
For Group 2 or P5 category locations medical IT (Ungrounded) system shall be used for circuits supplying medical electrical equipment and systems used for life support, surgical applications and other electrical equipment located in patient environment excluding circuits of operating tables, X-ray units and large equipment greater than 5 KVA.
The above excluded circuits of operating tables, X-ray units and large equipment greater than 5 KVA can be supplied from a grounded (TN-S) system with an RCD/ELCB with a rated residual-operating current not exceeding 30 mA. As a standard practice separate medical IT (Ungrounded) system shall be used for power supply sockets for electrical surgical & life support equipment and that for supplying to operation theatre lamps. Preferably different power source shall be used for both the independent medical IT system.
4.1 Design of Medical IT (Ungrounded) System:
The advantage of an ungrounded system is increased availability and continuity of power supply and reducing the magnitude of leakage current thereby avoiding shock and fire. Care shall be taken that the conventional touch voltage in the group2 location does not exceed 25 V by providing very low resistance earthing and equipotential bonding of non-active conductive parts
4.1.1 Medical IT (Ungrounded) System
The ungrounded power distribution system panel shall consist of the following. The input circuit breaker shall be double pole, single phase type. Rating of input CB shall be 300 VAC, 63A with breaking capacity 10KA. Only short circuit protection without overload protection shall be provided.
A single-phase isolating transformer according to IEC 61558-2-15 shall be provided with a maximum rated power of 10 kVA as specified in IEC 60364-7710. The isolation transformer shall be two winding with earthed isolation shield between the two windings. Further specifications are: secondary voltage of AC 250 V and a maximum transformer secondary leakage current of 0.5 mA to earth. In order to protect the transformer and the connecting leads between the primary and secondary terminals and the distribution bus against overload and over temperature, monitoring the load and temperature of the transformer is required. A visual and acoustic alarm shall be issued when the permissible load current and/or temperature are exceeded. For monitoring, a combination of temperature monitoring (PTC thermistors in the winding of the transformer) and current monitoring through CT shall be utilized in order to detect both a gradual heating of the transformer as well as the occurrence of a transient load when connecting high-capacity electrical equipment.
The transformer shall be fan cooled. The isolation transformer shall be installed near the critical medical room as close as possible. It shall be enclosed in cabinet or enclosures to prevent unintentional contact with live parts. Considering the load diversity in a typical OT, 10KVA isolation transformer is sufficient. If the total load in one medical room or location, like in a larger ICU, is more than 10 KVA then more than one transformer with individual transformer rating of 10 KVA maximum to cater to the loads shall be used.
The output circuit breaker shall be double pole, single phase type. Rating of output CB shall be 300 VAC, 63A with breaking capacity 10KA. Only short circuit protection without overload protection shall be provided.
In case of an ungrounded system, an insulation monitoring device shall be provided at the secondary side of the isolation transformer to indicate the occurrence of a first fault from live part to exposed-conductive-parts or to earth. This device shall initiate an audible and/or visual signal which shall continue as long as the fault persists. It is recommended that a first fault be eliminated with the shortest practicable delay
According to IEC 60364-7-710 & IS-NEC-SP-302011, an ungrounded (IT) system shall be equipped with an insulation monitoring device with the following requirements:
• The AC internal impedance shall be at least 100 kÙ
• The test voltage shall not be greater than DC 25 V
• The test current shall, even under fault conditions, not be greater than 1 mA
• The response value shall be ≥ 50 kÙ
• The indication shall take place, if the earth or wiring connection is lost
The measuring technology shall be universal for all ungrounded distribution systems with AC, AC/DC, DC loads. Further the measuring technology shall adapt to the changing load conditions in a modern OT, ICU and ICCU in hospital. The measuring technology along with special filtering system shall be highly accurate and very robust without generating spurious or missed alarms even in the presence of modern electronic and processor based equipment. Only DC voltage injection based measurement technology shall be avoided as it is prone to inaccurate measurements and spurious alarms leading to unreliable measurements.
For testing the insulation monitoring device a test button shall be provided directly at the device and in the remote alarm indicator and test combination. Self diagnostics shall be provided. In this way interruptions in connecting leads to the system and to earth are immediately recognized and indicated. The insulation monitoring devices shall comply with IEC 61557-8. Following indication & alarm shall be provided.
• A green lamp to indicate normal operation
• A yellow lamp and audible alarm to indicate insulation fault below set value
The number of load distribution feeders shall be limited for smaller size of distribution system. 12/16 nos. Of load feeder MCBs shall be provided for each isolation transformer. The MCBs shall be double pole single phase type. The rating shall be 300 VAC, 20 A maximum with breaking capacity 10KA. The load MCBs shall have both short circuit protection and overload protection.
In operation theatres & intensive care units, it is advantageous to use insulation fault location systems. The insulation fault location system is recommended as per IEC60364-4-41.Insulation fault location systems are recommended to be used in Group 2 locations like in OTs, ICUs & Premature Baby Rooms for the following reasons.
• A large number of socket-outlets are installed in an operation theatre/intensive care room so that the
detection of defective devices or faulty circuits involves a lot of time and costs.
• Often, the OT & intensive care bed cannot be used during fault location, since devices which support
vital body functions have to be disconnected. Therefore on-line fault location is recommended.
• Available personnel resources do not allow immediate fault location
The earth fault location system shall consist of on-line insulation monitor integrated with test pulse device, earth fault evaluator, number of special CTs(Sensors) depending on number of branch feeders.
The on-line insulation monitor shall continuously measure the insulation resistance of the entire galvanically connected ungrounded system including all connected loads. Whenever the insulation of the system drops below the preset value an alarm shall be generated and a test current driven by the system being monitored shall be generated alternately between each phase conductor and earth. This test current shall be detected selectively by means of special residual current transformers with evaluators. The design of the system shall be such that it rejects the noises in the power supply and distribution systems and shall be sensitive to the test current generated by the system. The system shall be robust and reliable without generating nuisance alarms. For safety reasons the test current shall be limited to 1 mA. The sensitivity of sensors shall be 0.1 mA minimum and measuring range between 0.1 mA – 1 mA. The earth fault location system shall comply with IEC61557-9.
The distribution cabinet/panel shall house the input CB, output CB, insulation monitor, load distribution MCBs, insulation fault location system. The cabinet shall be fabricated out of 14-gauge stainless steel or CRCA sheet steel in cubicle compartmentalized wall mounted, dust and vermin proof with reinforcement of suitable size angle iron, channels T sections and / or flats wherever necessary including 2 mm thick stainless steel door fitted with stainless screws (Degree of protection IP30 minimum). Knockouts shall be provided at the top / bottom of the panel. Panels shall be treated with all anti-corrosive process before painting. Paint shade shall be light grey or as approved. Cabinet/Box shall be with all components mounted and pre-wired. Incoming & outgoing cables shall be directly wired to Switches & Breakers or through terminals.
4.2 Remote Alarm Indicator for Medical/Technical Staff:
Due to insulation, load and temperature monitoring and fault location, the medical staff is informed
at an early stage, before a critical failure in the power supply occurs.
The following conditions shall be monitored and reported to the medical/technical staff by a remote alarm indicator and test combination:
1. If a faulty piece of equipment is plugged in, the system will detect the insulation fault and issue an alarm alerting the user to unplug the equipment and have it repaired.
2. Should excessive load be placed on the system, it will display the increasing load and will sound an alarm as the load approaches 100%.
3. Should an overload or fault cause the transformer temperature to rise above normal levels will sound an alarm and indicate the problem.
The information shall be indicated by an remote alarm indicator and test combination at a suitable place in the medical location so that it can be permanently monitored (audible and visual signals) by the medical staff (normal operation: green LED, alarm: yellow LEDs).
The information regarding the faulty feeder shall also be indicated in the remote alarm indicator for ease in maintenance and troubleshooting.
4.3 Environmental Qualification:
Ambient Temperature : – 10 deg.C to 55 deg.C
Relative Humidity : 95% non-condensing
Servo Control Voltage Stabilizer
General Description:
The specifications covers the requirement of Air Cooled Servo Controlled Voltage Stabilizer of X Nos of KVA
The SCVS in consideration basically consists of following power and control components.
- Buck – Boost Transformer.
- Variac with AC Servo motor drive.
- Solid state control card.
- Output contactor.
A three phase supply is given to system through SFU/MCCB. The Buck – Boost Transformer secondary is
connected in series with supply, and the output is taken from another lead of secondary. The primary of
Buck-Boost Transformer receives variable voltage through SerVomotor driven variac connected across the
same phase. The output voltage is sensed with electronic and accordingly command is given to the motor to
position the variac for giving corrected output voltage. The motor rotates in both the directions, reverse and
forward. A little time delay is needed to start with correction action to avoid the hunting due to surges and
transients.
Output of the Stabilizer is isolated by means of a Contactor.
Normal Mode:
The stabilizer has hot standby compatibility to ensure the redundancy where the connected loads are more critical. In this event the stabilizers are connected in series with one another. The master unit runs at full load, while the slave unit is merely switched on (idling). In case of master stabilizer fails the other healthy slave unit will supply the full load
Auto Mode:
The stabilizer is designed for and is suggested to used in auto mode. An operational amplifier senses the output and compares with reference level. The control card then automatically effects the corrective action with the help of SerVo motor and variac to buck or boost the incoming voltage so as to get well regulated output.
Manual Mode:
The unit can also be used in manual mode for some special applications. In manual mode, output voltage can be raise or lowered by a spring action switch provided on front panel. Any variation in output voltage due to load current or line variation can be corrected by using this switch in the event of failure of auto mode correction.
