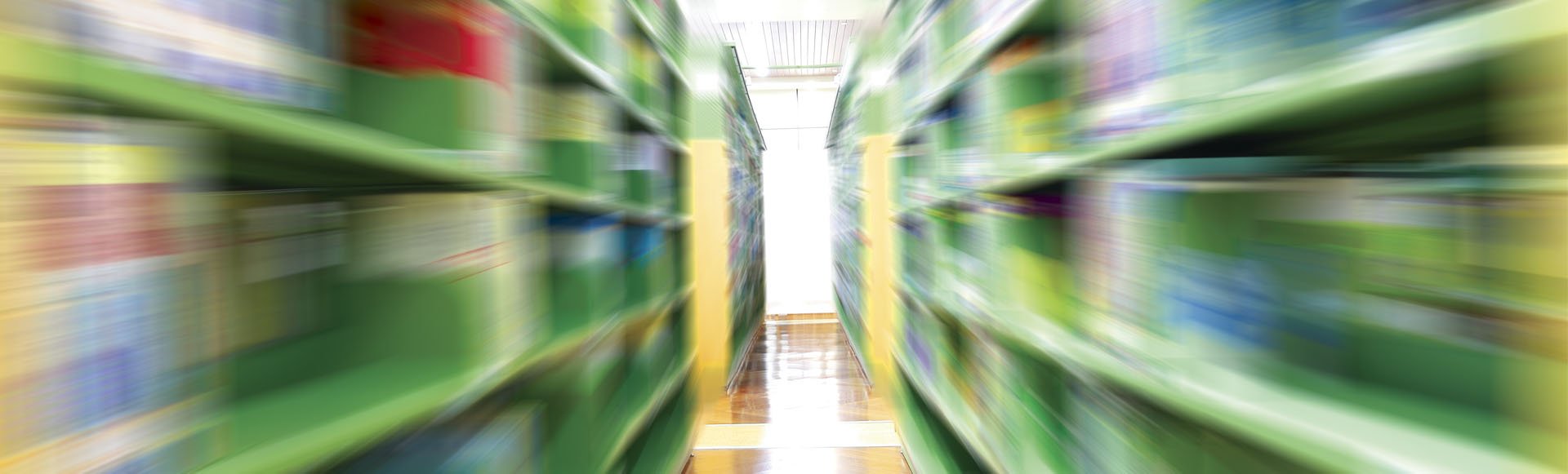
At Fuji Electric we develop products that maximize energy efficiency and lead to a responsible and sustainable society
When to replace the UPS
The question of when to replace an existing UPS comes up at some point of time for every user of UPS, be it a facility, IT, maintenance or operations manager. This question is typically triggered when there are increasing failures of the old UPS causing unplanned downtime or increasing costs of AMCs with multiple UPS OEMs or during an energy audit, which highlights the poor energy efficiency and utilization of the existing UPS. This white paper will provide the reasons for failures in UPS systems and also the factors to be considered for reduction of total cost of ownership when replacing an existing UPS.
Reliability bathtub curve
The bathtub curve is widely used in reliability engineering to ascertain the failure rate of a product and components used in the product over the useful life of the product. The probability of failure is described over three distinct timeframes by the bathtub curve.
1. Failure during startup or commissioning of the product: We sometimes see higher failures arising due to manufacturing defects, component defects, installation or site issues which results in “infant mortality”. Once these components are replaced and issues corrected, the failure rate decreases during normal operations.
2. Normal Operations: During the “useful life” of the product under normal operations, the failure rate is low and may be due to some random failures related to site issues.
3. End of Life: The failure rate increases due to “wear out” of the components due to continued use as the product nears the end of the design life have a wide range of failure modes based on the duration of operation and based on the operating conditions.
Relation of UPS system failures with bathtub curve: The Online UPS system typically consists of 3 major components
Rectifier to convert AC-DC and to charge the battery
Battery Energy storage device and will support in the event of power failure
Inverter Converts DC-AC, acts as a voltage source and will support the loads connected to it
UPS is primarily a power electronics product and consists of multiple electrical, electronics, electrochemical and mechanical components. UPS components have a wide range of failure modes based on duration of operation and based on the operating conditions.
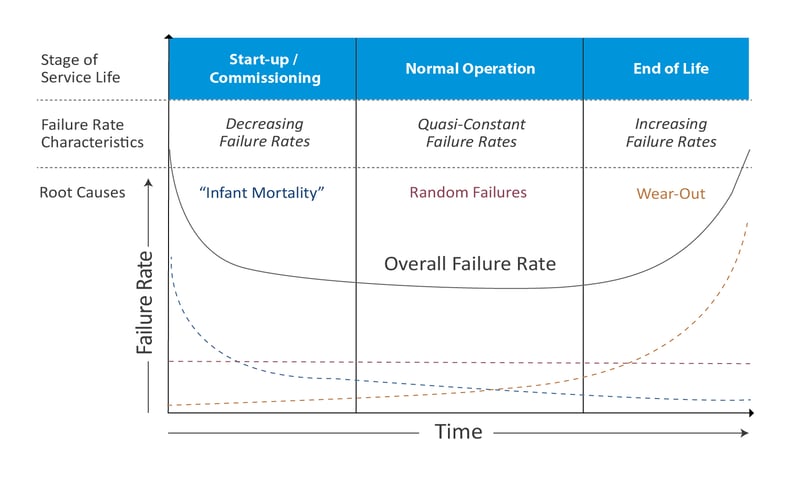
Typical life of components in UPS
Failure of electronic components can be caused by excess temperature, excess current or voltage, ionizing radiation, mechanical shock, stress or impact, and many other causes. In semiconductor devices, problems in the device package may cause failures due to contamination, mechanical stress of the device causing open or short circuits.
UPS System also has consumable parts that will age with use. Each component of a UPS will have different end of life when failure rates start increasing. Batteries are electro chemical components and are the key consumables associated with UPS and which requires replacement once in 3-4 years. Something which the manufacturers don’t disclose during the procurement process is the cost of replacement of other consumables like capacitors (electro chemical component) and fans (mechanical) which also need replacement based on the hours of operations.
Typical lifetime of major UPS components is given below but, the end of life can vary widely based on the components quality, designed lifetime and also the environmental conditions under which the UPS is operating.
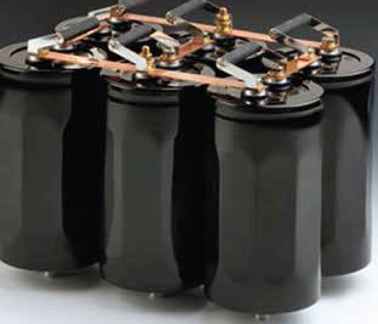
Capacitors used in UPS
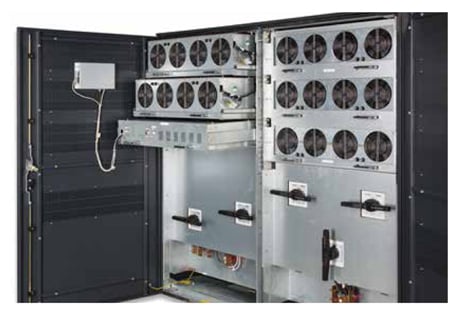
Fans used in UPS
Factors affecting the life of components
Defects in design, process, quality or part application, are the underlying cause of a failure or which initiates a process which, leads to failure. A brief overview of factors, which leads to failure of the components used in a UPS is listed below.
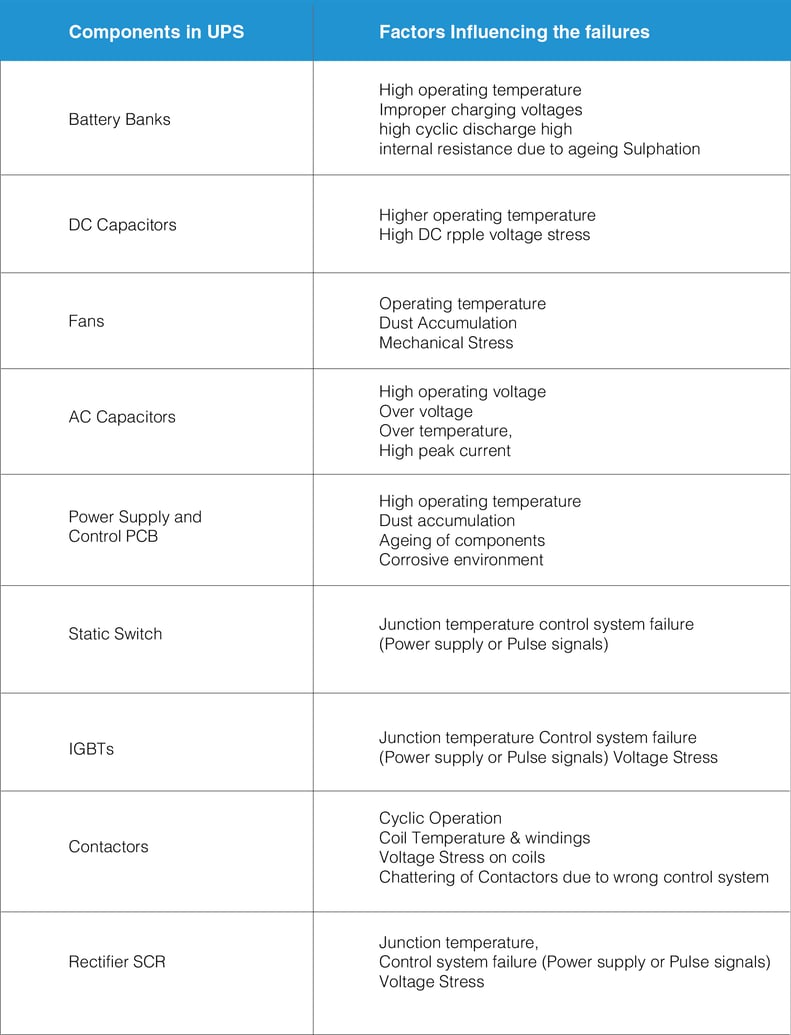
Impact of components failure for UPS and loads
Total cost of ownership
Total Cost of Ownership of a UPS System
The total cost of ownership of a UPS system can broadly be defined as consisting of capital costs and operating costs.
Capital costs (CapEx) includes the following:
- Purchase cost of UPS
- Cost of setting up the UPS and battery room including input and output switchgear and any environmental conditioning of the UPS room like the need for air conditioner
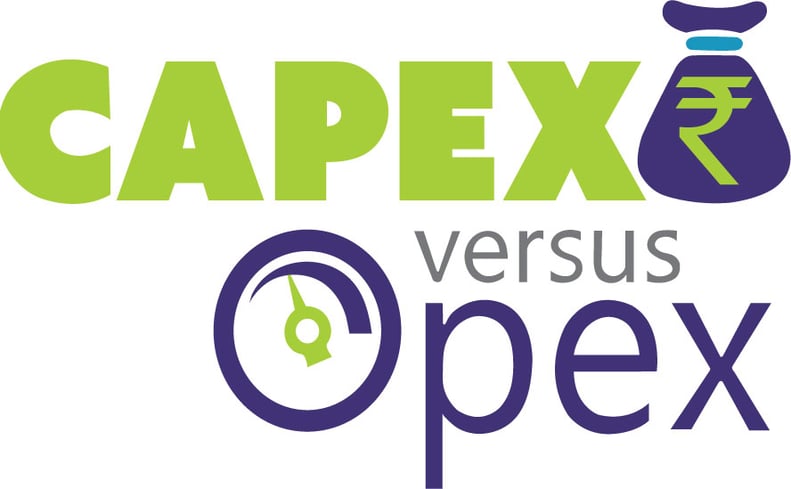
Operating costs(OpEx) include the following:
- Ongoing cost of AMC(Annual maintenance contract)
- Cost of Consumables replacement
- Cost of energy used by the UPS (Efficiency of the UPS)
- Loading on UPS
- Technology of UPS
- Compatibility for future expansion
Most of the UPS systems installed are under the Annual Maintenance Contract with the OEM. The AMC contracts typically exclude consumables replacement like battery, capacitors and fans. Also with the aging of the UPS system, frequency of failures will increase and the associated cost of downtime must also be accounted in operating costs apart from the AMC, consumable replacement costs and energy costs to operate an old UPS.
The service life of the UPS will also play a key role in deciding when to replace an UPS. The typical Three Phase UPS life is given below,
• Typical UPS service life5-7 Years
• Typical End of service life>10 Years
Sometimes it will be a better strategy to replace an old UPS before the end of life with a new UPS with current modern technology of UPS to help lower the total cost of ownership.
Factors influencing the decision of UPS replacement
Ongoing AMC cost
Annual Maintenance Contract(AMC) of UPS has now become a part of OpEx planning for all companies as the cost of downtime is much higher than the cost of AMC. The AMC price is decided based on certain percentage of the purchase price or based on fixed cost per KVA. These prices are almost fixed for the first 5 years after the warranty period at the time of purchasing the UPS (during the sales process) with a price escalation clause.
The AMC prices will be higher as the UPS ages. This is natural as we all know from the bathtub characteristic, when the UPS or the components reaches its end of life or with time, the probability of failure of components will increase.
Cost of energy(Efficiency of UPS)
The cost of energy is directly linked to efficiency of the UPS. If the efficiency is low, higher is the operating cost and with higher efficiency, the cost of energy will come down.
The efficiency of the UPS is related to
- Technology of UPS
- Percentage of loading on UPS
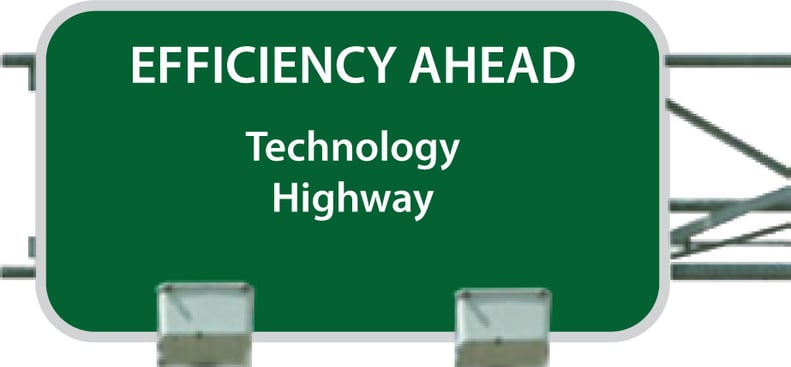
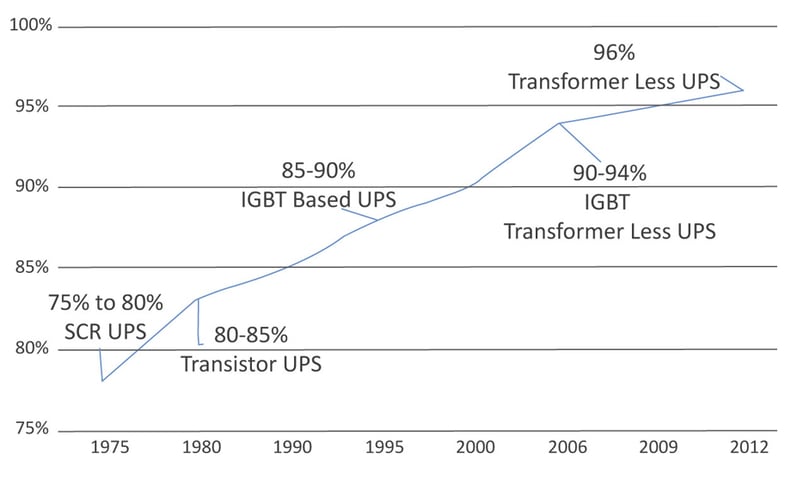
Technology of UPS
Over the last two decades, technological developments in UPS systems have mainly taken place in adapting advancements of Insulated Gate Bipolar Transistors (IGBT) which provides faster switching, increased ampacity (current handling capability), smaller sizes and overall cost reduction of UPS systems. These technology advancements have led to design of UPS systems with better input.
Performance, efficiency and reliability. Today an IGBT based UPS is available at 96% energy efficiency compared to 80-85% efficiency UPS manufactured two decades ago.
Percentage of loading on UPS
A UPS is rarely used at full rated load. In particular, for installations using redundant UPSs to provide continuous protection even when one of the units fails or is being serviced. The load is therefore generally lower than 100% of the rated capacity. Given that certain losses are practically constant, the efficiency will decrease with load level. It is important to avoid over sizing the UPS where normal operating power is very low compared to the UPS rating. At low load, the efficiency decreases.
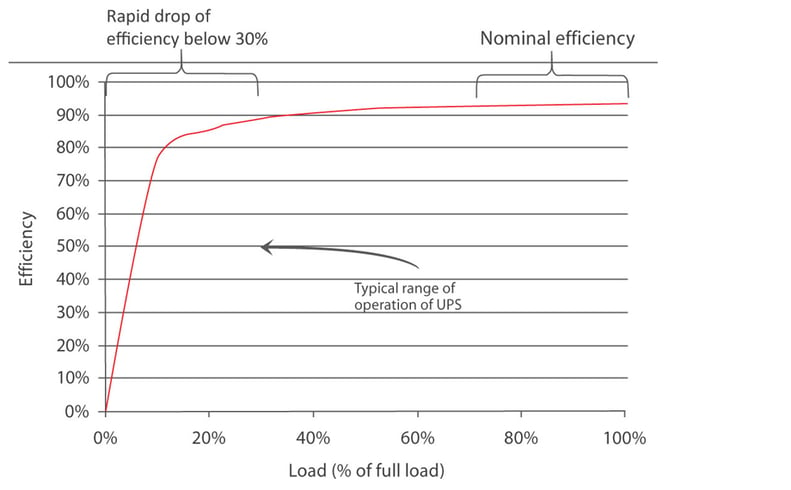
If the building was powered in a typical N+1 configuration, the UPS system, as a whole, would likely be running at 67% load. If the building was powered with a 2N configuration, the loading level would likely be around 42%. The efficiency of the first system, at 67% load, could be as high as 94%; the second system’s efficiency, at 42% load, would be 79-87%, using a typical Double Conversion online UPS system.
This would indicate that an intelligent system design would appropriately balance individual UPS loading levels with the needs of redundancy.
Compatibility for future expansion
How the load is expected to change over time will also influence the decision to maintain the same old UPS or to replace it with a new system. If the existing UPS system is at or near full load and future load growth is anticipated, then it is a better option to explore the possibility to replace the older UPS. The replacement UPS of modern technology can be chosen taking in consideration into future loads and compatibility with the existing infrastructure if the older system is >10 years.
If the systems are less than 10 years old, then the options to add UPS unit in a parallel system configuration must be explored. If the existing UPS capacity cannot be changed to meet the future requirements, then buying new is the only option ensuring that the new UPS System is compatible with the existing infrastructure.
On the other hand, if the existing units are lightly loaded, then buying new UPS may not be necessary. However, keep in mind that if the load is expected to continue to be a small percentage of the rated capacity, then it is possible to replace existing UPS with smaller units. Downsizing the UPS would improve efficiency, reduce the number of batteries needed, and likely lower AMC service costs. These gains should be noted in the financial analysis. The point is to be careful not to simply assume that a new UPS necessarily needs to be of a similar size as to what is currently installed.
Determining the future UPS load is an essential step in evaluating the options to keep, upgrade, or buy new. Having a reasonable estimation of future needs will determine, in part, whether or not the current UPS system
can meet future requirements.
Cost of downtime
Today’s businesses are more reliant on technology than ever before. When it comes time to consider installation of an emergency power source, it is crucial to understand cost of downtime. A few common items should be considered
- What is the impact of downtime on revenue ?
- What is the impact of downtime on productivity ?
- What is the impact on your organization’s reputation ?
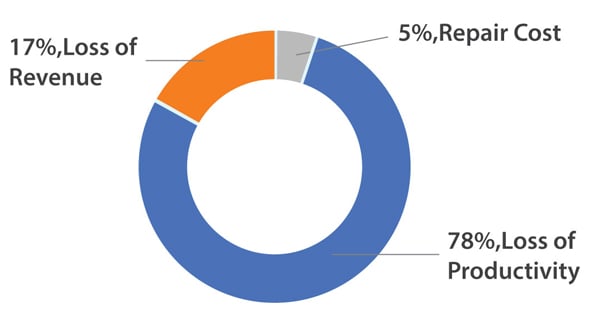
Cost of downtime can be represented by loss of production, data, credibility, and sometimes even lives (if it’s a critical Healthcare facility)
The cost of downtime can be simply calculated based on loss of revenue, loss of product and the cost to recover but, the indirect cost of business due to delayed delivery or quality issues which, may affect the brand is difficult to quantify.
Cost of Downtime (per hour) = Lost Revenue + Lost Productivity + Cost to recover + Cost of intangibles (i.e. reputation cost.)
Service life of UPS
Ageing of UPS plays a major role to as certain the deployment of a new system. To determine if your facility is a candidate for a new UPS system, consider these initial questions
- Is your UPS system more than 5-7 years old?
- Is the operating efficiency of an older system causing your utility bills to be a drag on your OpEx budget?
- Are critical parts becoming less available?
- Is servicing your system becoming more difficult?
- Is the current utilization level of your system too low or too high?
- Are the batteries / capacitors / fans due for replacement?
- Do you pay excessive maintenance cost?
- Do you encounter frequent failure of UPS components, leading to more downtime and associated high costs of unplanned downtime?
If you answered “yes” to one or more of these questions, there’s no time like the present to start investigating new UPS technologies. While cost is likely to be your first concern, you may be surprised at the operating savings a new system could provide.
If you answered “No” and assuming that the UPS has not come to end of Life and is meeting the load and run time requirements, one could choose to leave the old UPS in service and let it run till end of Life.
Summary : considerations for replacing old UPS
As discussed previously and from the below summary, it is evident that replacing an older UPS will be a good option for most UPSs after 5-7 years in operations.
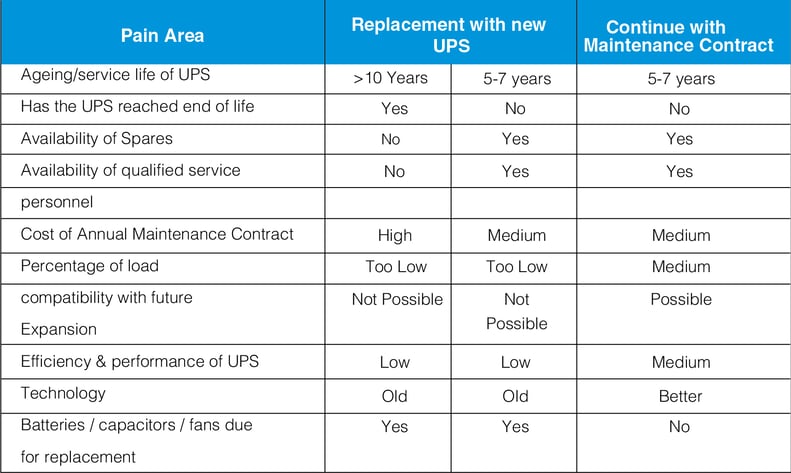
Case study 1
A comparative study on the total cost of ownership is illustrated for three different real life customer situations:
1. Resizing of UPS based on the actual load conditions
2. Replacement of existing UPS with a new UPS of the same capacity
3. Consolidation of multiple UPS (Decentralized) to common UPS (Centralized UPS)
Replacement of monolithic UPS with modular UPS
It is a common scenario in IT/ITES/ BPO /Data centre’s to see a load level of less than 40% on the UPS system due to:
- Over sizing of UPS during initial days considering future loads
- Excess redundancy buildup
- Replacement of the higher power old computers with CRT monitors to lower power TFT monitors
- Replacement of computer with virtual computers
- Replacement of dedicated servers to virtual servers
This has led to the low loads on the UPS which results in lower efficiency, higher losses and higher operating cost. Replacement with a modular UPS can have a payback period of less than three years as illustrated below.
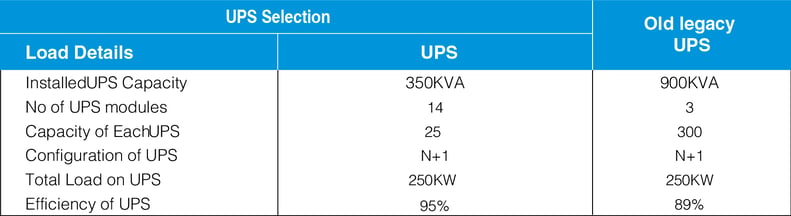
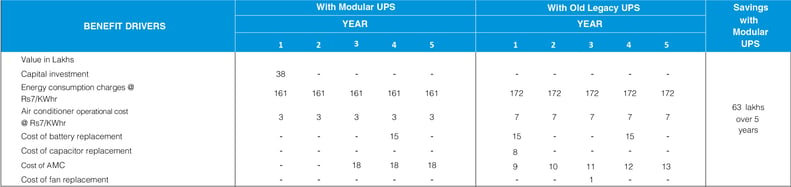
Case study 2
Replacement of monolithic UPS with new generation of monolithic UPS
Typically, in an industrial application like engineering, general manufacturing or process industry like food processing, plastic processing – a common UPS is used for a dedicated machine/process and the UPS will be at the maximum utilization rate. Indeed, these UPSs system could have been installed a long back (more than 7 years old) where the technological development in UPS was not advanced and typically these UPS has an efficiency of around 88-90%.
With the modern new technology in UPS system, the payback period is assured at 2.5 years if the older generation UPSs is replaced with modern new technology of UPS (as illustrated below).
The payback period could be much better if an Offline UPS with an efficiency of 98% is selected for certain applications. The selection of Offline UPS requires a detailed study of site conditions and load requirements.
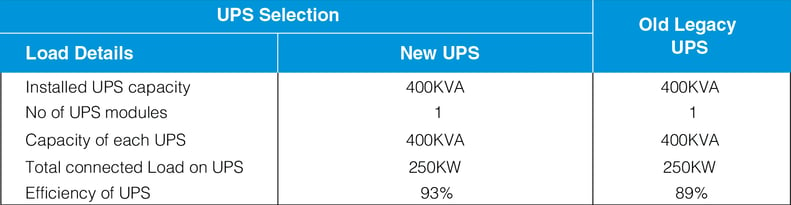
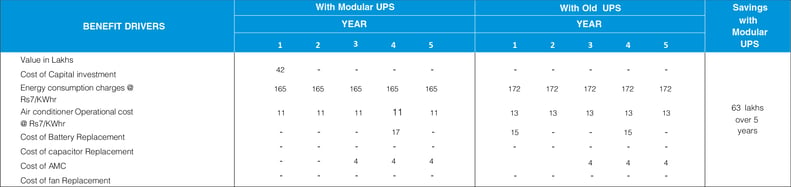
Case study 3
Replacement of multiple distributed UPS with a centralized UPS configuration
In an installation environment like hospitals, educational institutions there are lot of smaller UPSs spread across the campus as it was an easier solution to install the UPS as and where and when required as the institution grew.
With these decentralized solutions, the installation becomes easier, but on long run there is a challenge of managing these units and increased service cost. Typically, these smaller UPSs will have a service life of less than 5 years. Replacing than with a centralized UPS can have a payback period of less than three years as illustrated below.
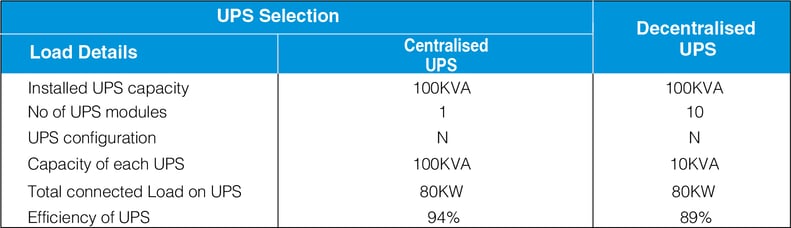
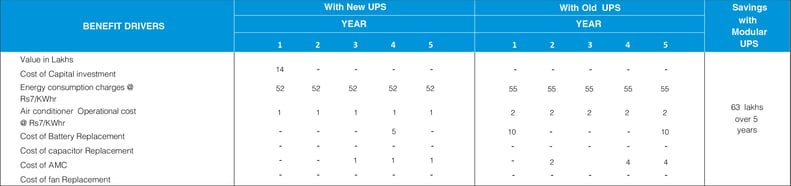
Conclusion
We have discussed the reasons for increase in UPS failure rate over time due to the ageing of the UPS components due to operational usage. Also discussed is the various operational costs involved with running of UPS including energy costs, AMC costs, replacement costs of consumables and cost of downtime due to increase in failure rates. Further the factors to be reviewed and considered before taking the decision to replace an old UPS are discussed. The considerations are also highlighted for different customer situations where the total cost of ownership can be reduced by replacing an older generation UPS with new, higher efficiency UPS systems. The replacement with new UPS systems will not only help to reduce operational costs but, also help avoid business downtime costs due to frequent failure of older systems.
Replacing UPS
- Reliability bathtub curve
- Typical life of components in UPS
- Factors affecting the life of components
- Impact of components failure for UPS and loads
- Total cost of ownership
- Factors influencing the decision of UPS replacement
- Ongoing AMC cost
- Cost of energy(Efficiency of UPS)
- Technology of UPS
- Percentage of loading on UPS
- Compatibility for future expansion
- Cost of downtime
- Service life of UPS
- Summary : considerations for replacing old UPS
- Case study 1
- Replacement of monolithic UPS with modular UPS
- Case study 2
- Replacement of monolithic UPS with new generation of monolithic UPS
- Case study 3
- Replacement of multiple distributed UPS with a centralized UPS configuration
- Conclusion